Work Processes are Everywhere
Whether we’re aware of it or not, there is a sequence of steps for every task we do - even simple activities like washing hands, brushing teeth, and making dinner. At work, some organizations use standard operating procedures (SOPs), which are just work processes that have been written down. Do we need an SOP to follow every morning and night to brush our teeth? Probably not. Do we need SOPs at work to ensure certain tasks are carried out consistently and accurately? Probably so. Process mapping is visual like the Cause Mapping® method, but instead of capturing causes, it captures the steps within a task.
Making Toast
Watch Tom Wujec’s excellent TED talk on problem-solving titled “Got a wicked problem? First, tell me how you make toast.” Wujec demonstrates how the simplest task of making toast can actually be carried out in an unlimited number of ways. Tom asks people to draw instructions for how to make toast using no words.
His exercise illustrates an interesting point. Different people have different perspectives on how toast is made. If you ask 20 different people to write instructions on how to do something, you’ll likely receive 20 different answers. Some instructions may be complicated and have many steps. Others may only have 3 to 5 steps. Each person may be able to accomplish the assigned task, but each person may use a different work process.
Different Process Maps
To demonstrate this, I asked three different people to build a process map for how they make toast. Here are the results.
Version 1: This Process Map is straightforward. It’s linear. There are no decision points. You just make toast.
Version 2: This process map is also straightforward. Although this version does offer an option to start over if one is not satisfied with the first attempt at making toast.
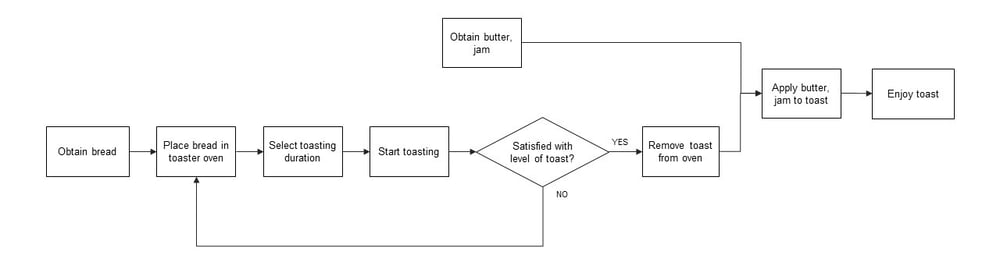
Version 3: This process map has more steps. In this household, there are different points of view for making toast: the dad’s method and the daughter’s method.
For a better view, click on the thumbnail to download the PDF of these different process flows.
Reduce Variation in Tasks
Variations in making toast are expected. However, do organizations want operational variations when initiating an emergency shut down or delivering medication? How important is it within your organization that some tasks are performed the same way every time? If it’s critical to your operations, then a process map is a great tool to help you document those tasks. When building a process map it’s essential to include the people who perform the task, both seasoned and new employees. Other technical experts need to be included also to ensure the work process is comprehensive and anticipates risks within the task.
Validating a Work Process
Each box on the map is one step of the process. After you have developed the process map, it needs to be tested. Have users review the steps while performing the task. Are details within a step being skipped? Are any steps confusing? It’s likely that the answer is yes. That’s okay. Process mapping is an iterative process. Develop the process map, test it, update it, and repeat. Do those three steps until you have evidence that the task can be completed consistently and accurately each time. Hey look! I made a process map for making a process map. It can be used for any task, from complex operations like launching a space shuttle or salvaging a cruise ship to simpler tasks like entering your time.
Problems Reveal Process Breakdowns
When conducting a root cause analysis of a problem terms like “procedure not followed” lead directly to a review of the work process. A process map makes it easier to identify where gaps or confusion in the work process exist. Once you identify these gaps they can be corrected. Understanding the cause-and-effect relationships as well as the steps in the work processes provide a more thorough root cause analysis. Once you identify why an incident happened, you can use a process map to show how work should be completed in the future.
Check out our blog “How reliable does your work process need to be?” to read more on this topic.